The Local newsletter is your free, daily guide to life in Colorado. For locals, by locals. Sign up today!
As essential businesses, most Colorado breweries and dispensaries continue to operate at some level under the state’s safer at home order. The ability to offer beer for pickup and delivery is certainly important to the state’s more than 400 craft breweries, which contributed approximately $3.2 billion dollars to Colorado’s economy in 2018, according to the Brewers Association (2019 numbers have yet to be released). But what receives less widespread attention is the environmental impact of brewing on a large scale: The American craft beer industry emits about half a billion metric tons of carbon dioxide into the atmosphere annually. Denver Beer Co. is trying to change that.
Beginning in early February, Denver Beer Co. and the Clinic, a medical and recreational cannabis company, launched a pilot project meant to capture the carbon dioxide generated during beer’s fermentation process and reuse it to stimulate marijuana plant growth. Austin-based Earthly Labs and the Colorado Department of Public Health and the Environment’s (CDPHE) Small Business Assistance Program joined the effort, bringing crucial technology to bear.
“Both industries are fairly resource intensive,” says Kaitlin Urso, an environmental consultant for CDPHE who helped spearhead the project by connecting Denver Beer Co. with the Clinic. Standard practice for craft breweries is to vent carbon dioxide byproduct straight into the atmosphere using what’s called a “blow-off arm.” But now, using Earthly Labs’ three-part system, Denver Beer Co. estimates it will be able to capture as much as 150,000 pounds of the carbon dioxide it produces each year for reuse at the Clinic.
Here’s how it works: The same “blow-off arm” that typically vents carbon dioxide from fermentation tanks into the atmosphere instead routes the gas to a pressurizing foam trap. The gas is then directed into a purifying box (dubbed “CiCi” by Earthly Labs), about the size of a refrigerator, that removes unwanted water, gases, acids, aromas, and volatile organic compounds (VOCs) before chilling the gas and converting it to a liquid, which allows the brewery to store a higher volume of the product.
Once the carbon dioxide has been captured and stored in this way, a certified driver trucks it nine miles from Denver Beer Co.’s Sunnyside production facility to the Clinic’s 6,600-square-foot cultivation center.
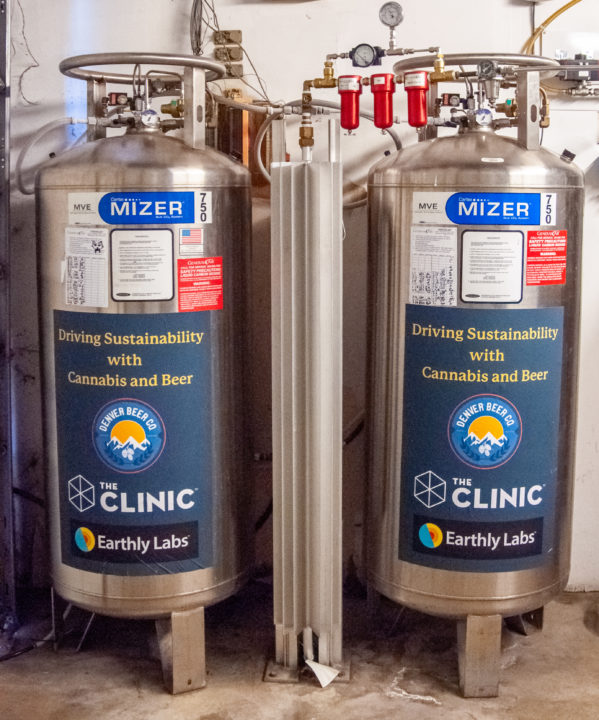
Why is it good to pump cannabis grow rooms with carbon dioxide anyway? When cannabis plants are grown indoors, the plants’ life cycle is condensed from between five and six months to four months. In order for the plants to perform under that shortened timeframe, they need supplemental carbon dioxide for photosynthesis to occur.
So, when that tank of recaptured Denver Beer Co. carbon dioxide arrives at the Clinic, it is hooked up to a system that converts it from a liquid back into a gas. The gas is released through a computerized regulation system into a 2,400-square-foot grow room dedicated for the pilot project.
The Clinic spends an estimated $15,000 per year on more than 110,000 pounds of manufactured carbon dioxide that is trucked in from companies across the United States; its current supplier requires the company to rent its release equipment in addition to charging steep transportation and delivery fees. By purchasing its own equipment for the release of Denver Beer Co.’s carbon dioxide, the Clinic estimates it will make back its initial investment in approximately 21 months with 15–20 percent total savings.
The pilot program is currently 14 weeks into its 16-week trial period. The Clinic is closely monitoring the growth of its trail plants in comparison to plants grown using carbon dioxide manufactured by the company’s regular supplier for performance indicators like overall health and growth rates. “The ultimate goal is to supplement the entire building with Denver Beer Co. carbon dioxide,” says Brian Cusworth, director of operations at the Clinic.
Denver Beer Co., like the Clinic, purchases commercial gas to inject into its beer in order to carbonate it. The installation of Earthly Labs’ capture technology now allows the brewery to carbonate its beer using its own carbon dioxide, which eliminates the need for both businesses to purchase the gas from a third-party supplier. “It’s really cool that our beer will now be made using 100 percent solar power and recaptured carbon dioxide,” says Denver Beer Co. co-founder Charlie Berger.
The capture of carbon dioxide by Denver Beer Co. allows for one industry’s greenhouse gas emissions to have a second life. “We’re inviting brewers to sell what would normally be an invisible waste product,” says Amy George, CEO of Earthly Labs. Although Earthly Labs’ technology is already in breweries across North America, its Denver project is the first capture and exchange project for the company.
“I’m so proud that [Denver Beer Co. and the Clinic] were able to prove that this is a viable system, not only from the environmental standpoint where we’re reducing excessive CO2 emissions, but proving it from an economic standpoint as well,” says Urso.
What does this all mean for consumers? In addition to reducing Denver’s greenhouse gas emissions, there’s the potential to produce better tasting beer. “We did some tasting panels using the gas we buy and the gas that we reclaimed, and we realized there was a significant difference. A lot of people preferred the beer made with the reclaimed carbon dioxide,” says Berger. “It’s all relative. But it’s our job to do our part when we can.”